Waste Management
Retail activities such as delivering goods to DCs and stores and selling goods generate large volumes of waste, with packaging being the main source. Fix Price recognises the need to minimise its waste generation and implements a responsible waste management approach.
The Company generates several types of waste:
- solid (Hazard Classes 4 and 5, low-hazard and non-hazardous waste);
- recyclables (cardboard and stretch film);
- office equipment (Hazard Class 4).
Solid waste volumes generated by the Company are calculated according to the norms set by regional waste disposal operators. Although we can only have a limited influence on the regional operators’ calculations, if we see that the norms they apply are much higher than the actual waste volumes generated at the Company’s facilities, we negotiate with them to adjust those norms where possible.
The packaging waste from goods sold at Fix Price stores is mostly cardboard and polyethylene film, both of which can be recycled. We strive to boost the volume of recyclables collected in stores and returned to DCs to be sent for recycling. Our stores are equipped with polyethylene and cardboard presses to help us return the maximum amount of waste back to DCs. Store managers are responsible for maintaining records of the amount of waste compressed. Towards the end of 2021, Fix Price launched an initiative to improve how stretch film and cardboard are returned to our DCs. We developed tailored targets for each store regarding the amount of recyclables to be sent to DCs depending on store revenue and the type of press installed. If a store underperforms against its targets, we conduct an internal audit. In early 2022, we fine-tuned the software that helps us control recyclable turnover. At the end of the reporting year, we saw the total amount of waste sent for recycling increase by 45% year‑on‑year.
2020 | 2021 | 2022 | |
---|---|---|---|
Total amount of waste | 158,477 | 141,958 | 168,354 |
Total amount of waste sent for recycling: | 17,352 | 19,411 | 28,236 |
Cardboard | 15,928 | 17,581 | 24,939 |
Stretch film | 1,424 | 1,829 | 3,297 |
We strive to minimise waste generation in our DCs and thus, foster the use of returnable packaging. We re-use pallets 4 to 5 times and then repair them for further use. We also recondition batteries or send them for special recycling after 3–5 years of use. To formalise the waste-return and pallet-repair process, we developed and introduced guidelines for returning pallets and recyclables to DCs. The guidelines regulate the procedures for preparing returnable and recyclable items for transport back from stores to DCs, as well as for maintaining records for recyclables and pallets.
Since 2020, we have been using electronic document interchange (EDI) to reduce the use of non-renewable resources, which enabled the Company to significantly decrease paper consumption.
The Results of Using EDI in 2022
EDI was deployed for:
of counterparties of the franchising development unit
of counterparties in the non-commercial procurement segment
of leaseholders
of goods supplies
We managed to significantly reduce the time taken to sign documents, i.e. from 2–3 weeks down to
The Company streamlined document interchange. In 2022, the number of EDI-based and processed documents increased 6 times in comparison with the period prior to the EDI launch.
In 2022, Fix Price managed to decrease its paper consumption related to document flow by 32% y-o-y
We launched an EDI hotline for our counterparties in the non-commercial segment
Fix Price secured a top-three finish at the 2022 PRO EDO competition for the best EDI project. Judged by members of the business community, the competition is organised by SKB Kontur, one of the largest vendors of EDI-focused IT solutions for business
In 2022, Fix Price introduced new eco-friendly bags containing 40% recycled polyethylene. The bags are not made from any PVC or bio additives and can also be recycled themselves. In 2022, the bags were extremely popular among our customers and continue to gain traction
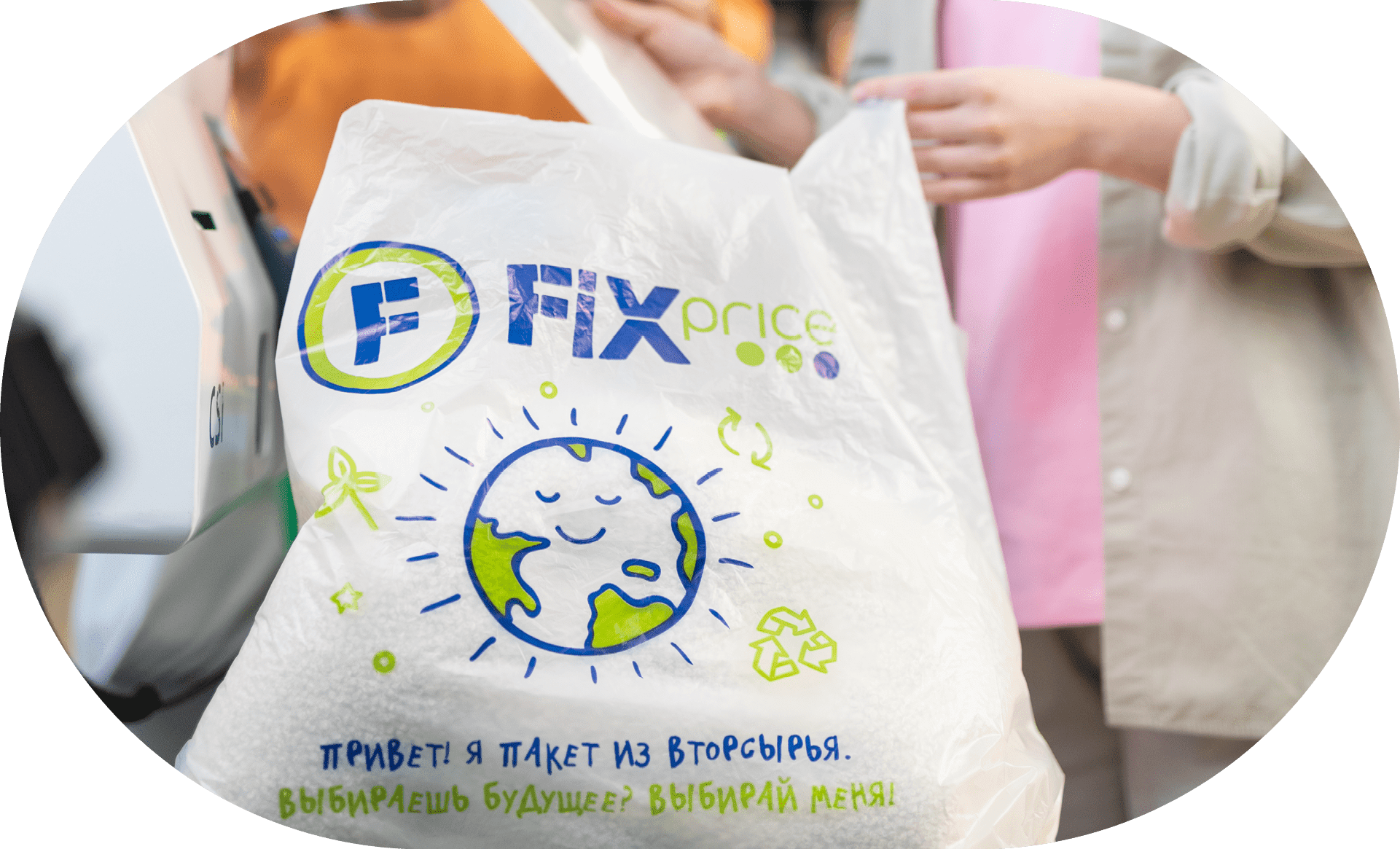
The Company is pushing ahead with its initiative for reconditioning and reusing IT equipment, including everything from computer system units, laptops and cash registers to cameras, multifunctional devices, data terminals, and audio amplifiers. The IT Department keeps broken and used equipment and repairs or upgrades it, installing wherever necessary parts taken from other devices in order to reuse the refurbished items. This enabled us to reduce the volume of non-functional computer equipment and only generate e-waste if the equipment could not be repaired.
We are deeply involved in the development of our private-label products. This includes packaging: we seek to use the least amount of wrapping possible while maximising the use of recyclable materials and mono-materials wherever possible.
We are also focused on increasing transparency and the availability of information on the packaging of private-label SKUs. On each element of combined packaging customers can find a separate Mobius loop symbol that keeps them informed of how to responsibly sort waste.
Moreover, in 2022, we switched to paperless receipts at checkout which helped reduce paper waste.